UpdateEmission Monitoring on LNG Vessels š¢ š±
Our emissions modelling engineer on a mission to monitor emissions
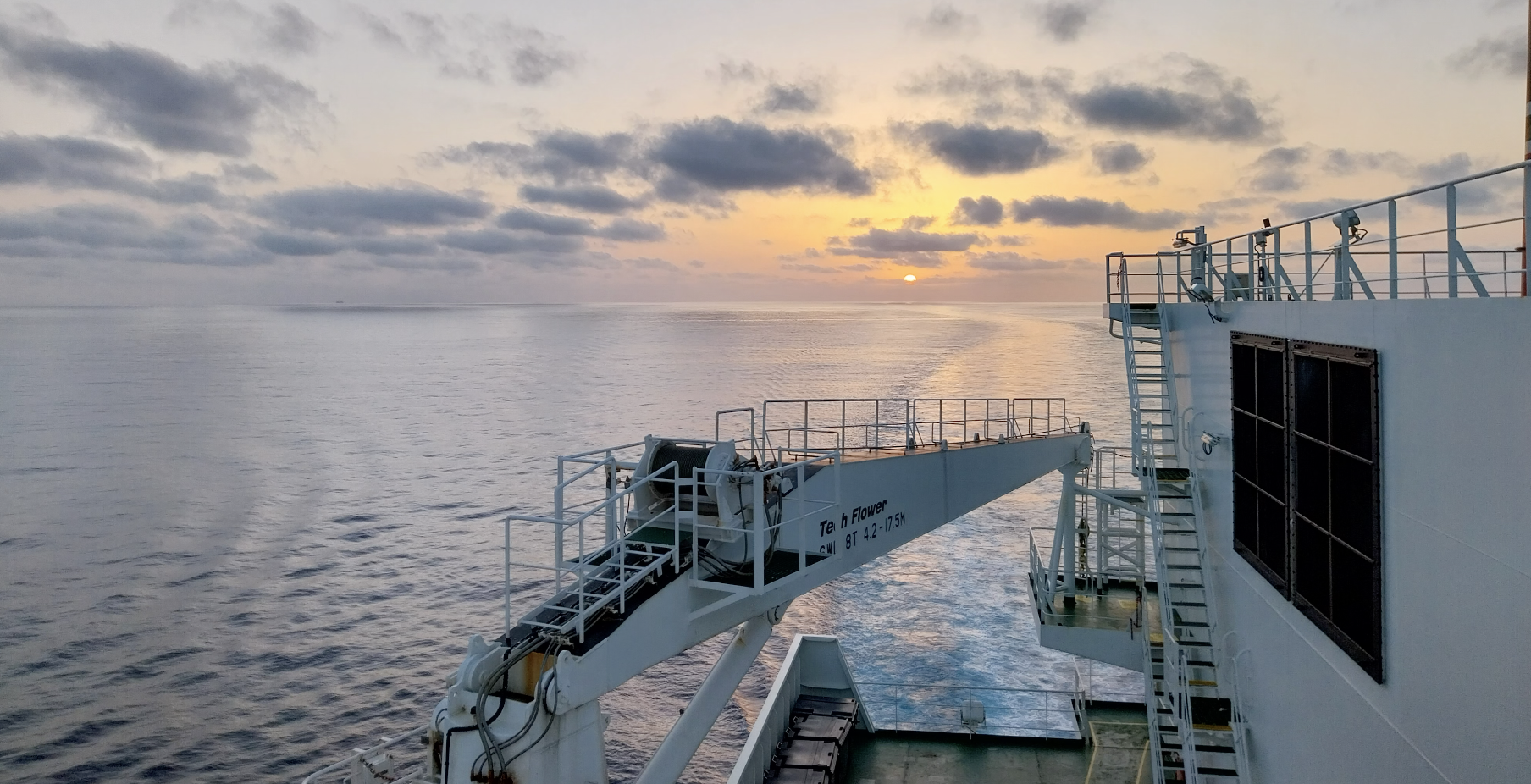
Last month, our emissions modelling engineer, Knut IbƦk Topp Lindenhoff, was on a mission to monitor the emissions released by an LNG vessel across the Mediterranean Sea. Throughout the trip, Knut was primarily in the engine room, working with gas measurement equipment to capture data on methane emissions from their engines.
āThe most exciting part of this trip was the opportunity to see the engine room in real life, and experience how everything on board the vessel is connectedā - Knut
Why this matters?
Methane is a much more potent greenhouse gas in comparison to carbon dioxide due to its high absorptivity. Therefore, it is crucial to burn off methane during operations to minimise its climate impact. Measuring emissions on LNG vessels is significant to our customers commitment to reducing greenhouse gas effects, especially under the OGMP 2.0 framework set to measure and reduce emissions. On this trip, Knutās duty was to account for the amount of methane the vessel was releasing, for each of the respective engines. This helps us minimise the greenhouse gas effects.
Successfull stack measurments
The measurements were successfully performed on several loads for all engines. The quality of the measurements was kept high by using a newly designed filtering system and by the use of nitrogen for flush and high-grade N2 from onboard the ship. The quality of the measurements was controlled by comparing background measurements and by performing a span check. The measurements were only conducted when the content of sod particles were low, ensuring that the mirrors were kept clear.
A big acknowledgement goes to the entire team, who helped improve the measurements with good flanges and being very cooperative.
āUpon arrival on the vessel, I quickly felt as I was a part of the engine team. The social bond definitely helps making the measurements faster and with higher quality. It was a big pleasure to meet all the amazing people aboard the vessel.ā - Knut
Why PEMS and not CEMS?
Unlike traditional emissions monitoring (CEMS), PEMS is designed to be more reliable, offering a robust solution that does not need any physical maintenance.
The combustion of pilot fuel and diesel fuel results in a larger amount of solid particles and sod in the exhaust compared with natural gas. As a result, CEMS installed on vessels often require extensive maintenance and can break down within a few days, necessitating repairs by specialists.
PEMS only needs data from a couple of hours of direct measurements of the exhaust, to be validated and calibrated. Once calibrated, the system uses live process data from the vessel to perform first-principle simulations, effectively creating a digital twin. This allows PEMS to calculate various emissions and performance parameters, including methane, NOx, CO2, CO, SOx, efficiency, and more, without ongoing physical intervention
PEMS Solution for LNG engines
In the PEMS systems, there are several models of different parts of the combustion unit with several models. Each model is a large differential equations system that combines theoretical energy and mass balance with knowledge of the specific engine.The stack measurements are then compared with the model simulation, and the parameters are fine-tuned for the particular unit. The combustion systems are solved at each given time interval, and emissions are computed based on a large amount of process data and results from the previous simulation.